Job ID: 21604076
Job Category: Operations
Location: Hamel, MN
Job Title: Director, Maintenance Excellence
FLSA Status: Exempt
Department: Technical Support and Maintenance
Reports to: SVP, Contract Services, Americas and Global OEM
Flex Work Eligible! This position qualifies for the Flexible Work Policy. Employees receive 75 workdays annually to work remote! The initial amount of days is prorated for the first year based on start date.
GENERAL DESCRIPTION / PURPOSE:
The Director, Maintenance Excellence is responsible for all aspects of developing and supporting the processes, systems, and business tools used in maintaining Loram equipment on a global scale. This role leads the strategic vision, planning, and execution of global maintenance team defining standards and practices with a focus on total lifecycle cost control, safety and operational optimization. This role drives innovation and continuous improvement in maintenance planning, implementing best-in-class predictive and preventive strategies, ensuring the organization maximizes asset performance while minimizing costs. This position is focused on standardizing global maintenance processes, fostering a culture of safety and accountability, and delivering measurable improvements in operational performance.
ESSENTIAL JOB FUNCTIONS:
Leadership and Talent Development
- Collaborate with Human Resources to build and maintain robust talent pipelines that align with current and future organizational needs, including succession planning for critical roles.
- Partner with Learning and Development teams to design and implement comprehensive training programs that emphasize technical expertise, maintenance planning best practices, and leadership skills.
- Cultivate a culture of accountability, collaboration, and innovation by mentoring team members and fostering cross-functional engagement.
Safety and Operational Excellence
- Champion a culture of safety by integrating it as a core value within all levels of operations and decision-making.
- Develop and implement global maintenance standards and a centralized maintenance management system and tools to ensuring consistency and alignment across all regions and facilities.
- Collaborate with engineering and maintenance teams to establish and improve predictive and preventive maintenance strategies, driving at least 98% equipment reliability.
- Establish and track key performance metrics (e.g., leading and lagging indicators) that utilizes real-time data to measure the effectiveness of maintenance programs and identify areas for corrective action or improvement.
- Lead initiatives to align maintenance practices with long-term operational and financial objectives, balancing cost, reliability, and safety considerations.
Business and Financial Management
- Oversee maintenance-related budgets, including forecasting, cost management, and capital improvement planning, ensuring alignment with organizational goals.
- Identify and execute cost-saving opportunities without compromising operational reliability, safety, or quality.
- Collaborate with procurement and supply chain teams to optimize inventory management, balancing reliability requirements with cost-efficiency.
- Conduct market analysis to stay informed about emerging maintenance technologies, competitive trends, and industry best practices, leveraging insights to recommend strategic investments.
Communications
- Motivate and inspire excellence through effective written and verbal communications with the executive team, operations leadership team, customers and other LMW team members
- Develop and maintain strong relationships with key stakeholders, including customers, vendors, and internal partners, to foster a collaborative environment of continuous improvement.
REQUIRED QUALIFICATIONS:
Education: Bachelors degree in Reliability Engineering, Engineering, Business, or related degree
Experience: Minimum of 10 years of experience in maintenance operations, reliability engineering, or asset management, with at least 5 years in a leadership role.
- Experience in managing budgets, forecasting capital expenditures, and optimizing cost control in maintenance operations.
- Experienced in continuous improvement methodologies, root cause analysis and asset data analysis
- Working knowledge of maintenance & inventory management systems.
- Data management skills demonstrated through proven ability to use statistical analysis tools as well as interpret
and communicate the results of the analysis
- Experience working directly with customers
- Experience traveling both internationally and independently.
10+ years of experience managing a heavy equipment maintenance operation, 5+ years of managing two or more direct reports
Licenses/Certifications: Maintain railroad safety training and certifications
*In lieu of education for 14+years or equivalent combination of education and experience in maintenance operations, reliability engineering, or asset management, with at least 5 years in a leadership role.
PREFERRED QUALIFICATIONS:
Education: Masters degree or other technical degree
Licenses/Certifications: Lean Six Sigma Green Belt
WORKING CONDITIONS:
The physical demands described here are representative of those that must be met by an employee to successfully perform the essential functions of the role. Reasonable accommodations may be made to enable individuals with disabilities to perform the essential functions.
- Office deskwork, requiring sitting, walking, using phone & computer
- May lift up to 30 lbs. occasionally
- 30% or more travel including international
- Can tolerate variable and sometimes challenging conditions during visits or inspections of company equipment in a railroad environment
Benefits for this role include a comprehensive package with company-sponsored medical, dental, and vision insurance; Health Savings Account (HSA) and Flexible Spending Account (FSA) options; wellness programs; basic life and AD&D insurance; voluntary life insurance; company paid short-term and long-term disability coverage; 401(k) retirement plan including an employer match of 150% up to the first 6% you contribute to the Plan; Employee Assistance Program (EAP); behavioral health support; and leaves of absence. Additional benefits include tuition reimbursement, payroll charity contributions, adoption assistance and optional plans such as legal, critical illness, and hospitalization.
Loram determines compensation based on factors such as skills, competencies, education, and/or experience. Certain positions may be eligible for an annual bonus and paid time off in addition to base compensation.
Starting pay for the position is between $142,800 – $182,000
Loram is an Equal Opportunity Employer and will make all employment-related decisions without regard to race, color, religion, creed, sex, sexual orientation, gender identity, national origin, age, disability, marital status, familial status, status with regard to public assistance, membership or activity in a local commission, protected veteran status, or any other status protected by applicable law.
Revised February 2025
#LI-ONSITE
#LI-KK1
Job ID: 21604076
Job Category: Operations
Location: Hamel, MN
DESCRIPTION
Job Title: Director, Maintenance Excellence
FLSA Status: Exempt
Department: Technical Support and Maintenance
Reports to: SVP, Contract Services, Americas and Global OEM
Flex Work Eligible! This position qualifies for the Flexible Work Policy. Employees receive 75 workdays annually to work remote! The initial amount of days is prorated for the first year based on start date.
GENERAL DESCRIPTION / PURPOSE:
The Director, Maintenance Excellence is responsible for all aspects of developing and supporting the processes, systems, and business tools used in maintaining Loram equipment on a global scale. This role leads the strategic vision, planning, and execution of global maintenance team defining standards and practices with a focus on total lifecycle cost control, safety and operational optimization. This role drives innovation and continuous improvement in maintenance planning, implementing best-in-class predictive and preventive strategies, ensuring the organization maximizes asset performance while minimizing costs. This position is focused on standardizing global maintenance processes, fostering a culture of safety and accountability, and delivering measurable improvements in operational performance.
ESSENTIAL JOB FUNCTIONS:
Leadership and Talent Development
- Collaborate with Human Resources to build and maintain robust talent pipelines that align with current and future organizational needs, including succession planning for critical roles.
- Partner with Learning and Development teams to design and implement comprehensive training programs that emphasize technical expertise, maintenance planning best practices, and leadership skills.
- Cultivate a culture of accountability, collaboration, and innovation by mentoring team members and fostering cross-functional engagement.
Safety and Operational Excellence
- Champion a culture of safety by integrating it as a core value within all levels of operations and decision-making.
- Develop and implement global maintenance standards and a centralized maintenance management system and tools to ensuring consistency and alignment across all regions and facilities.
- Collaborate with engineering and maintenance teams to establish and improve predictive and preventive maintenance strategies, driving at least 98% equipment reliability.
- Establish and track key performance metrics (e.g., leading and lagging indicators) that utilizes real-time data to measure the effectiveness of maintenance programs and identify areas for corrective action or improvement.
- Lead initiatives to align maintenance practices with long-term operational and financial objectives, balancing cost, reliability, and safety considerations.
Business and Financial Management
- Oversee maintenance-related budgets, including forecasting, cost management, and capital improvement planning, ensuring alignment with organizational goals.
- Identify and execute cost-saving opportunities without compromising operational reliability, safety, or quality.
- Collaborate with procurement and supply chain teams to optimize inventory management, balancing reliability requirements with cost-efficiency.
- Conduct market analysis to stay informed about emerging maintenance technologies, competitive trends, and industry best practices, leveraging insights to recommend strategic investments.
Communications
- Motivate and inspire excellence through effective written and verbal communications with the executive team, operations leadership team, customers and other LMW team members
- Develop and maintain strong relationships with key stakeholders, including customers, vendors, and internal partners, to foster a collaborative environment of continuous improvement.
QUALIFICATIONS
REQUIRED QUALIFICATIONS:
Education: Bachelors degree in Reliability Engineering, Engineering, Business, or related degree
Experience: Minimum of 10 years of experience in maintenance operations, reliability engineering, or asset management, with at least 5 years in a leadership role.
- Experience in managing budgets, forecasting capital expenditures, and optimizing cost control in maintenance operations.
- Experienced in continuous improvement methodologies, root cause analysis and asset data analysis
- Working knowledge of maintenance & inventory management systems.
- Data management skills demonstrated through proven ability to use statistical analysis tools as well as interpret
and communicate the results of the analysis
- Experience working directly with customers
- Experience traveling both internationally and independently.
10+ years of experience managing a heavy equipment maintenance operation, 5+ years of managing two or more direct reports
Licenses/Certifications: Maintain railroad safety training and certifications
*In lieu of education for 14+years or equivalent combination of education and experience in maintenance operations, reliability engineering, or asset management, with at least 5 years in a leadership role.
PREFERRED QUALIFICATIONS:
Education: Masters degree or other technical degree
Licenses/Certifications: Lean Six Sigma Green Belt
WORKING CONDITIONS:
The physical demands described here are representative of those that must be met by an employee to successfully perform the essential functions of the role. Reasonable accommodations may be made to enable individuals with disabilities to perform the essential functions.
- Office deskwork, requiring sitting, walking, using phone & computer
- May lift up to 30 lbs. occasionally
- 30% or more travel including international
- Can tolerate variable and sometimes challenging conditions during visits or inspections of company equipment in a railroad environment
Benefits for this role include a comprehensive package with company-sponsored medical, dental, and vision insurance; Health Savings Account (HSA) and Flexible Spending Account (FSA) options; wellness programs; basic life and AD&D insurance; voluntary life insurance; company paid short-term and long-term disability coverage; 401(k) retirement plan including an employer match of 150% up to the first 6% you contribute to the Plan; Employee Assistance Program (EAP); behavioral health support; and leaves of absence. Additional benefits include tuition reimbursement, payroll charity contributions, adoption assistance and optional plans such as legal, critical illness, and hospitalization.
Loram determines compensation based on factors such as skills, competencies, education, and/or experience. Certain positions may be eligible for an annual bonus and paid time off in addition to base compensation.
Starting pay for the position is between $142,800 – $182,000
Loram is an Equal Opportunity Employer and will make all employment-related decisions without regard to race, color, religion, creed, sex, sexual orientation, gender identity, national origin, age, disability, marital status, familial status, status with regard to public assistance, membership or activity in a local commission, protected veteran status, or any other status protected by applicable law.
Revised February 2025
#LI-ONSITE
#LI-KK1
ABOUT

Based in Hamel, Minnesota, Loram Maintenance of Way, Inc. designs and builds some of the most sophisticated railway maintenance equipment in the world, delivering high quality products and services to our global customers. This is made possible by employees who are passionate about delivering advanced equipment, innovative solutions, and unrivaled customer service.
For more information about Loram go to:
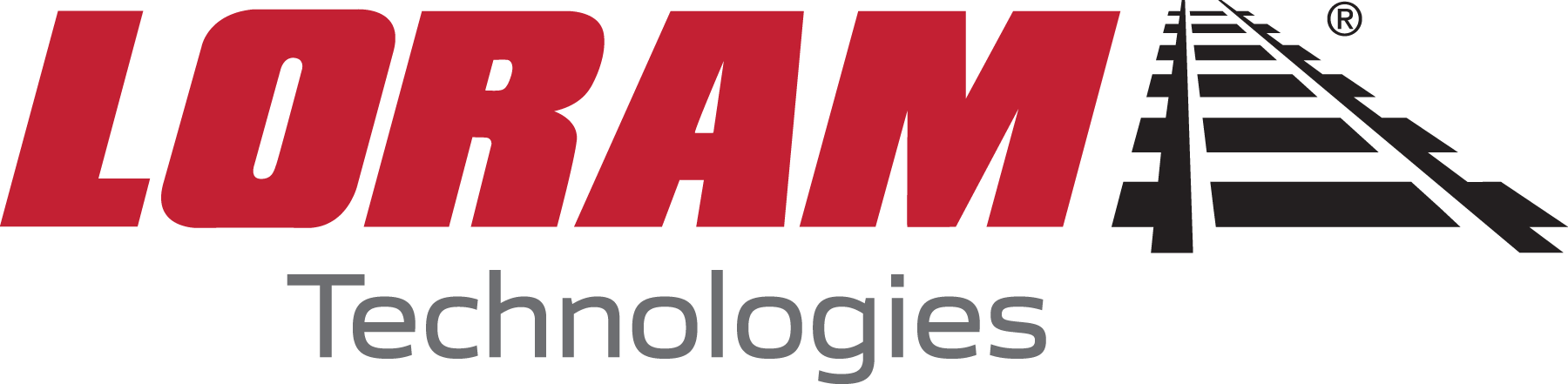
Based in Georgetown, Texas, Loram Technologies, Inc. provides innovative solutions for the railroad industry. From our friction management application systems to our Aurora® track inspection systems, our products are technologically advanced, safer, more efficient, and more productive than traditional maintenance methods.
For more information about LTI go to:
http://www.loramtechnologies.com
Loram is proud to be an Equal Opportunity Employer of Minorities, Females, Protected Veterans, and Individuals with Disabilities.
RECEIVE JOB ALERTS
Be the first to know about the jobs that are right for you. Set your criteria and sign up now.
About the area
Find out more about Hamel, MN